The specialists of the RST-Invent company developed an RFID system for monitoring and tracking raw materials at the production lines of the “Philip Morris Izhora” factory in the Leningrad Region.
As part of the project, RST-Invent company developed, manufactured and implemented a number of customized RFID solutions in the customer’s assembly lines, which made it possible to monitor online the compliance of the components supplied to the line with the type of product. The system made it possible to exclude the influence of the human factor on the quality of tobacco products manufactured by the enterprise. Also, the full integration of the developed hardware-software complex with the customer’s MES system was carried out.
The constructed RFID system helped automate the control of technological processes in the production of cigarette products, and increased transparency and efficiency in process control. Thus, the system minimized human involvement in the quality control of the product and, as a result, prevented errors associated with the use of raw materials not intended for the manufacture of certain products.
Working principle
To control the correctness of the supply of semi-finished filters to production lines in the FTS system, RFID tags are used that are attached to a plastic or cardboard tray.
The FTS system assigns a unique identifier (code) to each tray when filling it with semi-finished filters. To do this, all production lines that produce semi-finished products are equipped with RFID modules (readers) that automatically record the identifier in the memory of the RFID tag of the tray, based on a job received from MES.
The identifier not only uniquely determines the type of semi-finished product in the tray, but also contains a code for a specific type of future cigarette filter.
The control of the correctness of the supply of semi-finished products is carried out at the site of receipt of trays of finished cigarette filters on the production lines. The RFID readers installed on the lines compare the filter code in the RFID tag with the code received from the MES system.
In case of coincidence of codes, semi-finished products are recycled. In case of an error, the line stops automatically, the semi-finished products are not loaded, and the operator receives a warning in the form of a light signal.
If it is necessary to repack the semi-finished product from a cardboard tray to a plastic one, the FTS system automatically transfers all identification information to the RFID tag of the plastic tray.
Each RFID tag in the FTS database is assigned a unique identifier. When loading the tray with semi-finished filters, the corresponding filter code is written to the RFID tag. When semi-finished products are fed to the production line, the filter code is read from the RFID tag memory.
The filter code from the MES system is transferred to the FTS database and then sent to all RFID readers of the production lines. Information about loading or unloading from a tray of a particular semi-finished product on the production line is stored in the FTS database, from which it is subsequently transferred to the customer’s MES system.
RFID tags and equipment
Specially for the Philip Morris project, a special series of TwinTag RFID tags with an increased memory capacity was developed and produced, made in the form of a sticker. This label is unified for marking both types of trays: cardboard and plastic. The label provides the ability to install various models of UHF chips. The RFID tag is designed to meet the requirements of stable registration of objects in various planes (3D format), and its characteristics provide stable reading on various production lines.
In addition, the RST-MAR RFID reader has been developed, featuring unique design antennas designed specifically for the Philip Morris project. Antennas are equipped with sensors to monitor the presence of a tray on the production line. For installation on production lines, antennas are equipped with magnetic mount. Installation of antennas is carried out without making changes to the design of production lines.
Information about the company «Philip Morris Izhora»:
CJSC «Philip Morris Izhora» is a full-production company, from primary processing of tobacco raw materials to the production and packaging of high-quality cigarettes.
This is the largest «Philip Morris International» factory in the world in terms of production capacity.
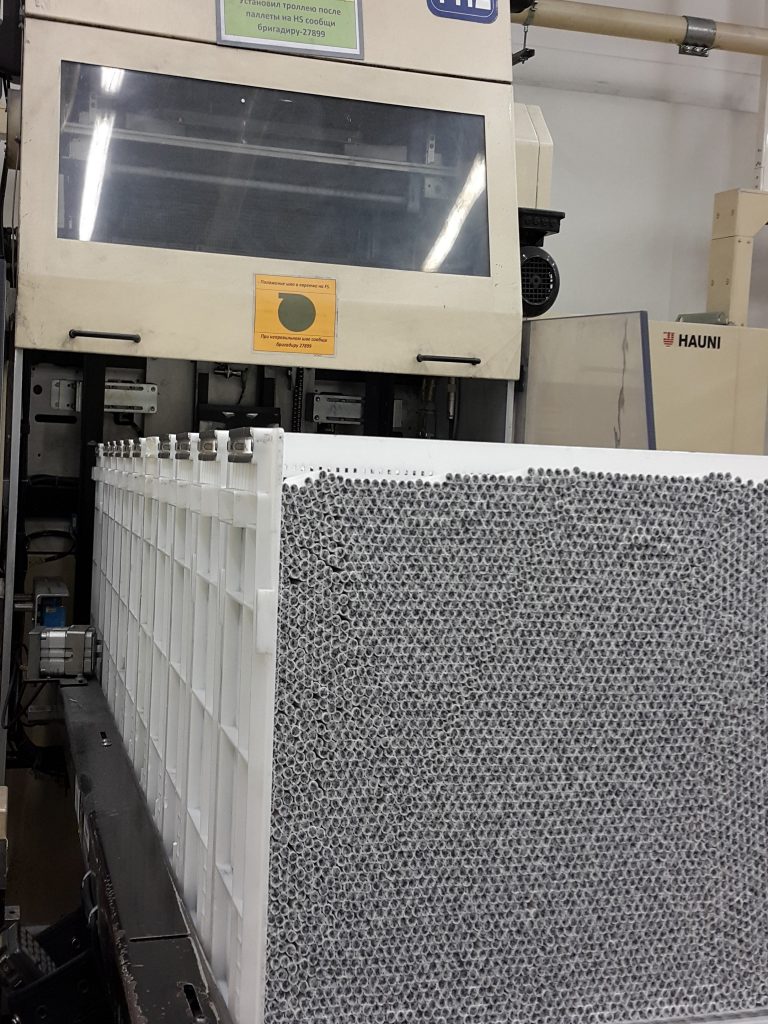
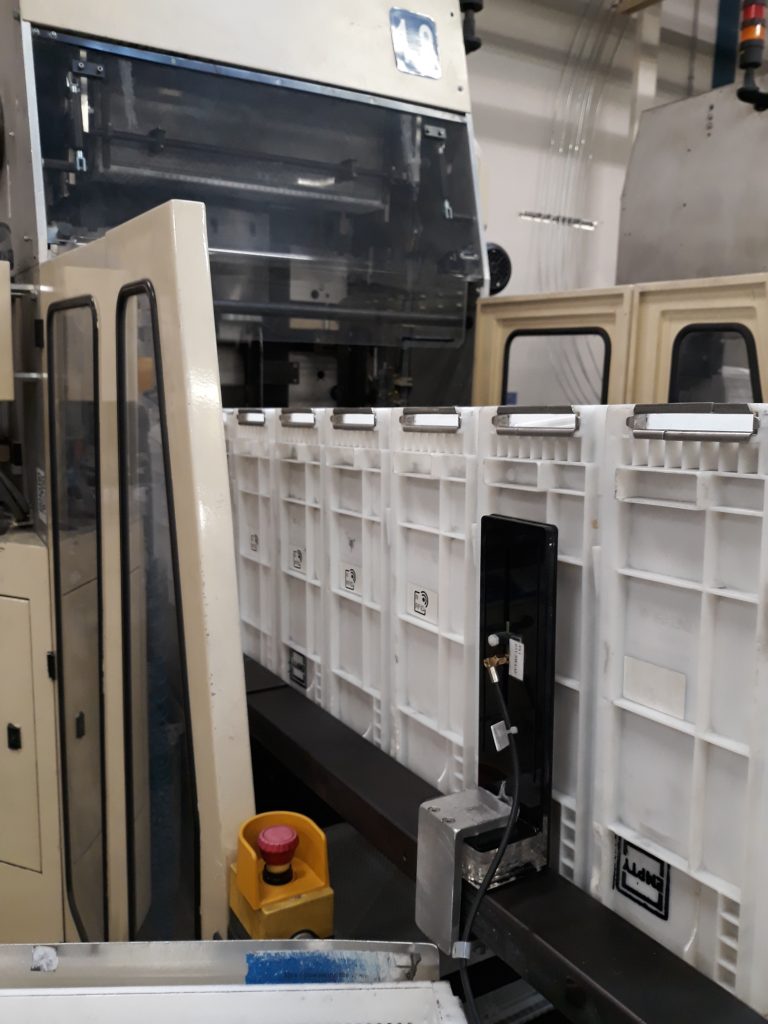
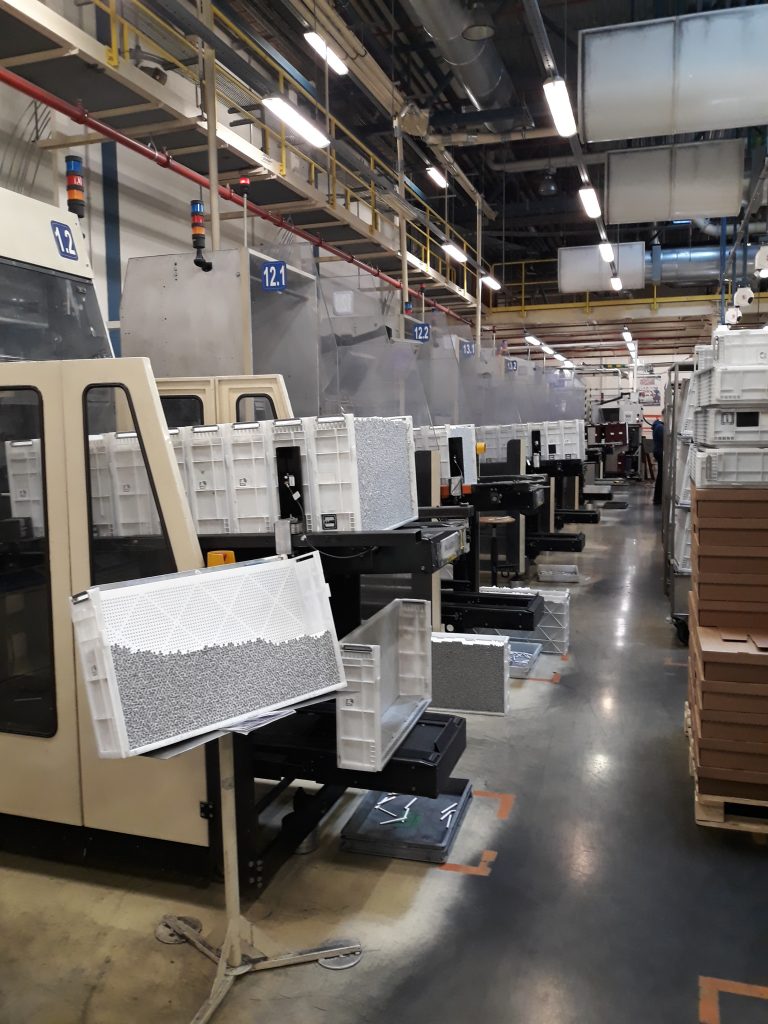